LIGHTHOUSE RESTORATION
Keer takes great pride in taking part in lighthouse restoration for some of the world's most important lighthouses. Until the latter half of the 20th century most lighthouses were originally fitted with Fresnel lenses. Some of these jewels of the sea are constructed from hundreds of glass prisms. Each prism requires high precision to send a beam of light over miles of ocean. Since 2003, Keer has restored numerous belt-lens and prism geometries for the unique Makapu’u hyper-radial light (Oahu, Hawaii), the Diamond Head light (Honolulu, Hawaii), and the Ponce de Leon Inlet light (Ponce Inlet, Florida).
Contact us today for more information on our lighthouse restoration services, and read about a unique project of ours below.
(photo courtesy of James Woodward)
Restoration process
Story behind the lens
Over the years, a classification system for designating the size of Fresnel lighthouse lenses was implemented (1st order being the largest and 8th order the smallest). In the late 1800s, two larger sizes were added, the largest being the hyper-radial Fresnel lens. Out of the almost twenty thousand lighthouses ever built, only 31 hyper-radial lenses were ever made. Today the whereabouts of only 22 are known, and there are only 12 left functioning in lighthouse towers to protect mariners today. Of these, the Makapu'u Point light is the largest configuration of any hyper-radial light. In 1968, it was damaged by gunfire. Two of the belt lenses were destroyed by the impact. In 2008, the U.S. Coast Guard decided to restore the Makapu'u Point light and the Diamond Head light in Honolulu, Hawaii. In total, 13 lens components needed to be replaced. Keer Glass was contracted to undertake the reproduction of the glass. Lighthouse lenses are made predominantly of radial glass prisms; however, some have "belt"-shaped glass components as well. The belt lenses that we machined for the Makapu'u Point light are the largest lens components of any lighthouse ever made.
US Coast Guard
Makapu’u hyper-radial light (Oahu, HI)
(photo courtesy of James Woodward)
US Coast Guard
Diamond Head light (Honolulu, Hawaii)
View from inside the Makapu'u Point hyper-radial light (photo courtesy of James Woodward)
Making of the hyper-radial belt lens for the Makapu'u point lighthouse
Damaged original hyper-radial belt lens
Though the geometry is not particularly complex, the required scale and precision for the two curved Makapu'u belt-lenses presented a considerable challenge. We needed to design and produce custom molds, fixtures, and tooling throughout the multi-stepped process. The first step was to make a clay model of the lens. An investment mold was made from this, and the glass was cast. Next, custom diamond tools were created for milling. After machining, the lenses were lapped. Finally, the lenses were hand-polished.
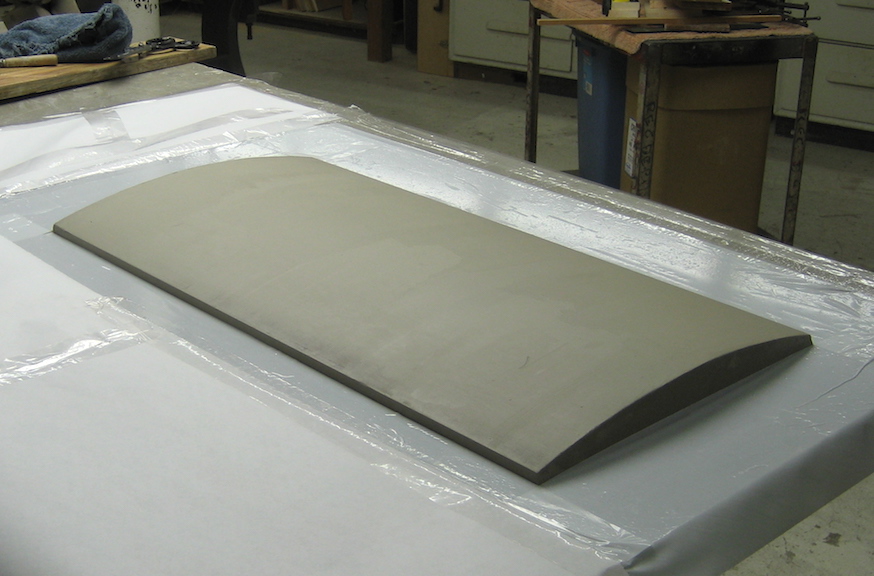
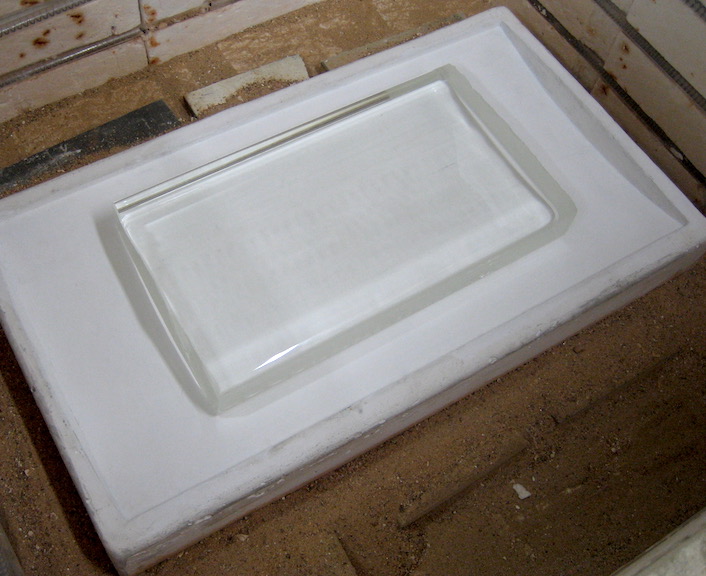
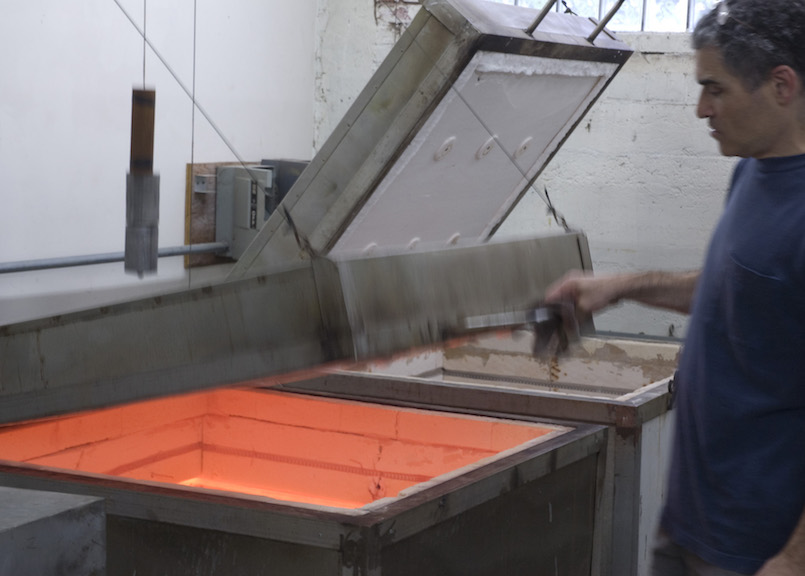
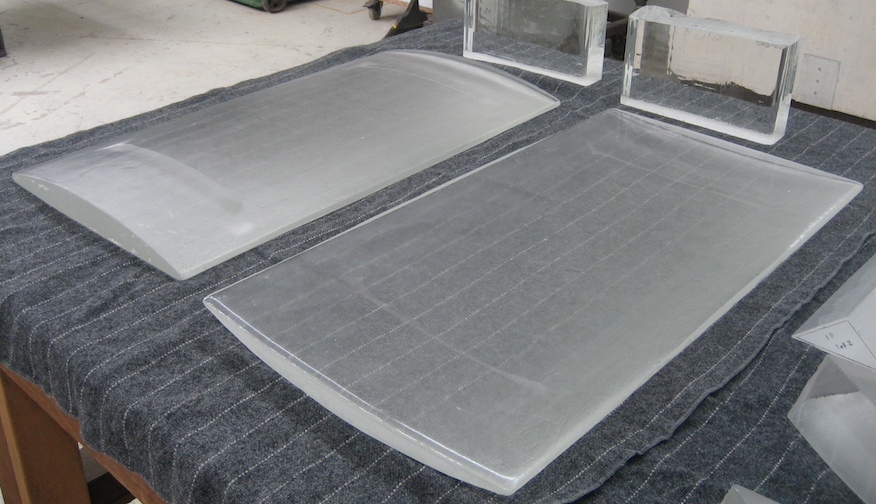
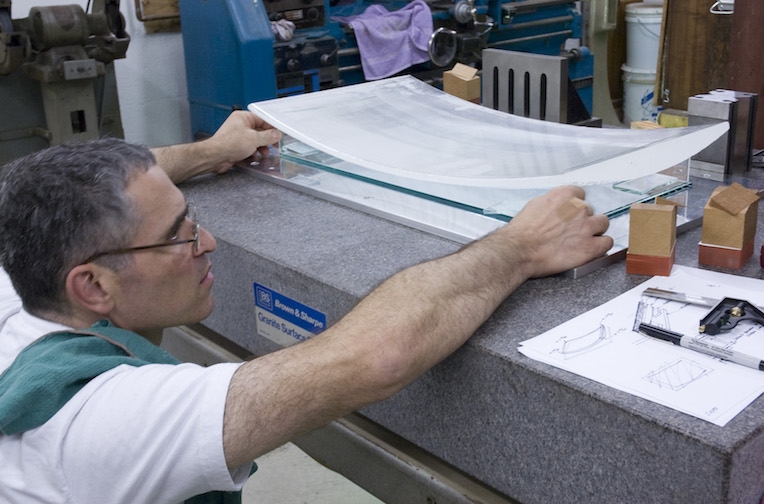
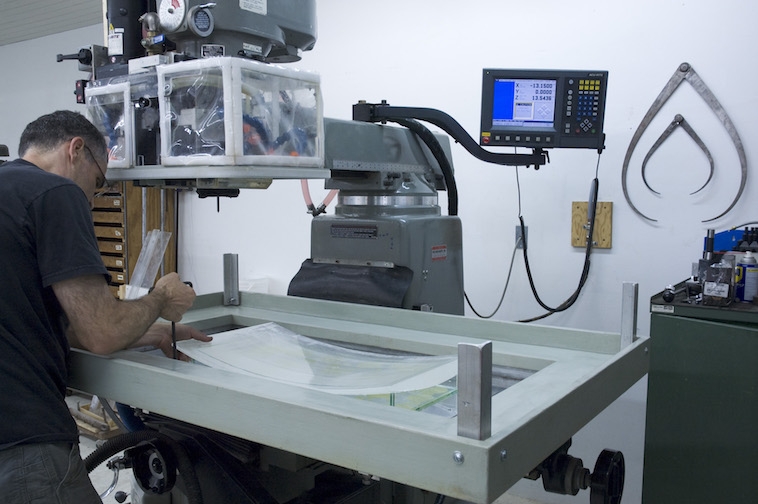
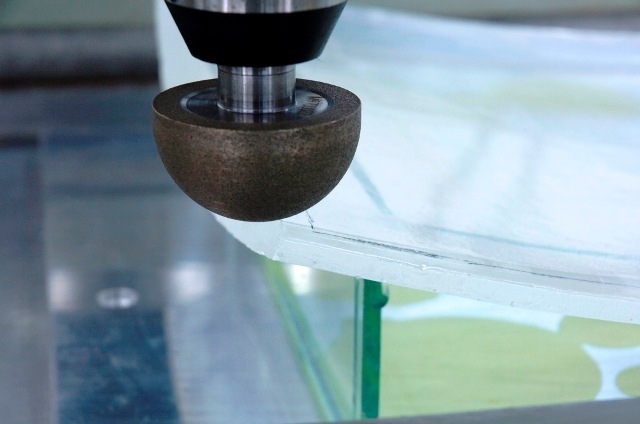
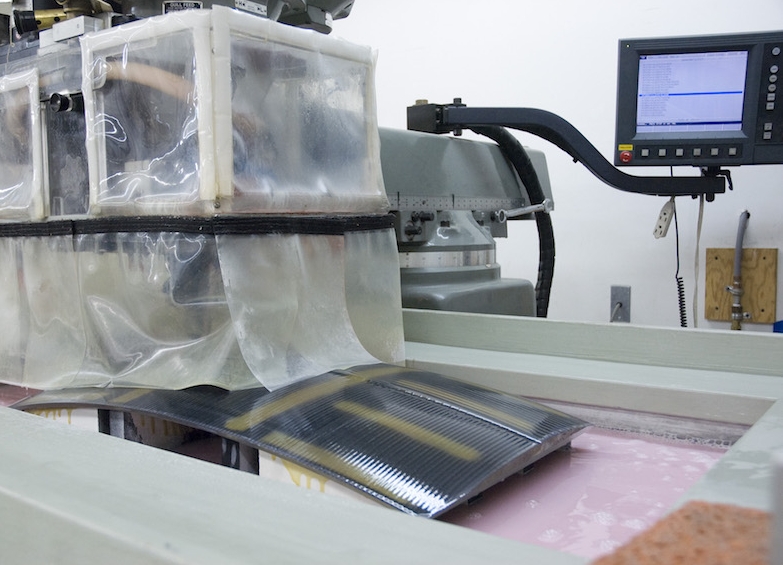
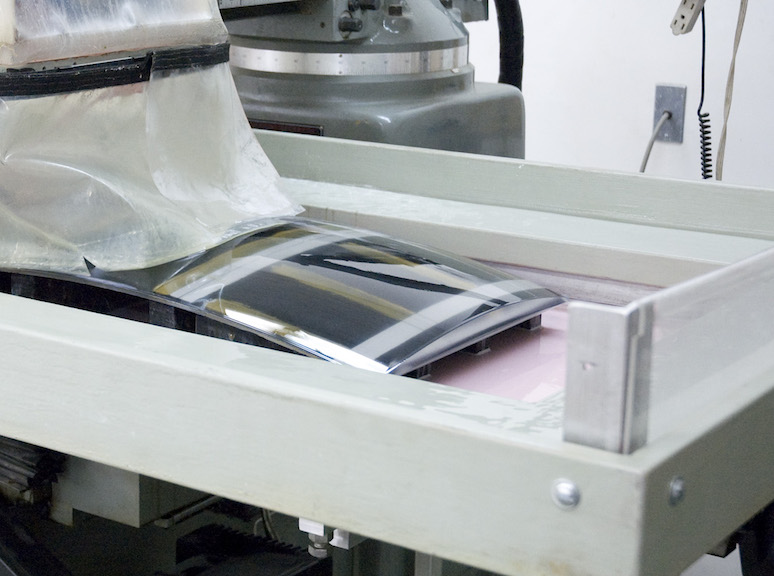
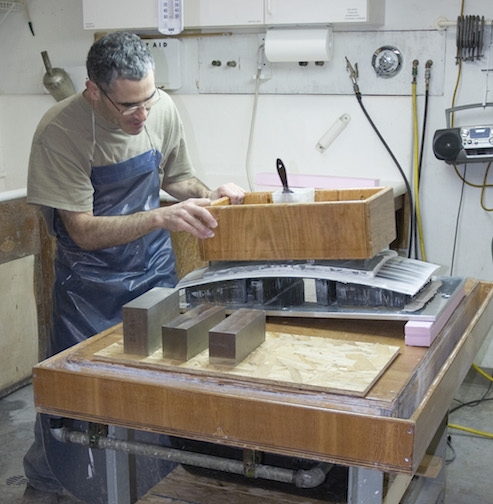
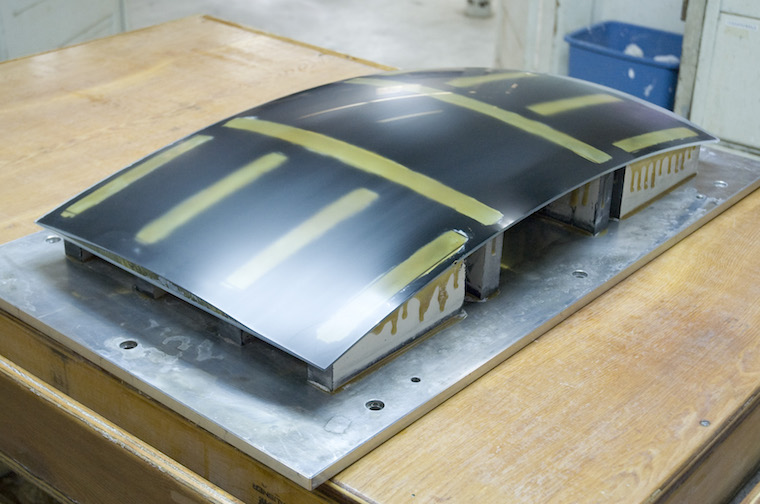
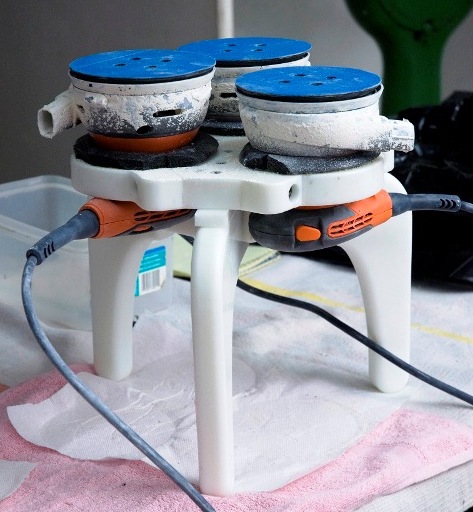
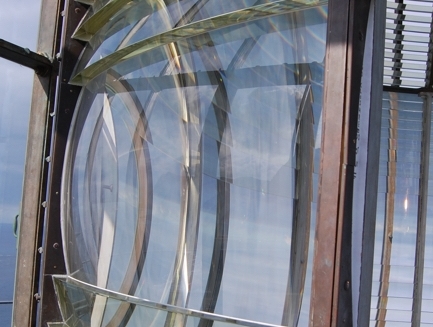
Making of prisms for Makapu'u and Diamond head
Diamond Head light with panels containing damaged prisms removed
Damaged original prism, Diamond Head light
We did a lot of research on traditional lighthouse prism manufacturing methods prior to taking on this project. This included traveling to England to visit a museum which had one of the original machines for producing lighthouse glass. While we gained a lot of valuable technical information, in the end we choose the more contemporary technology of CNC machining with diamond tools, which is a highly efficient way to create precise glass components. To start, virtual models of the desired lens geometry were generated on the computer. Glass blanks were then cast and mounted on the CNC mill. After machining, further surface refinement was achieved by lapping the lenses with glass laps. To do this, we built a semi-automated programmable lapping station capable of adjusting to the various geometries we needed to produce. For the final step, we polished the lapped surfaces by hand with cerium oxide and water on a felt wheel.
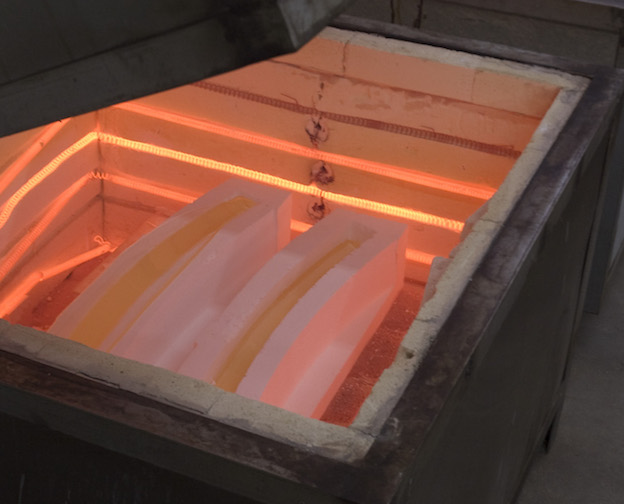
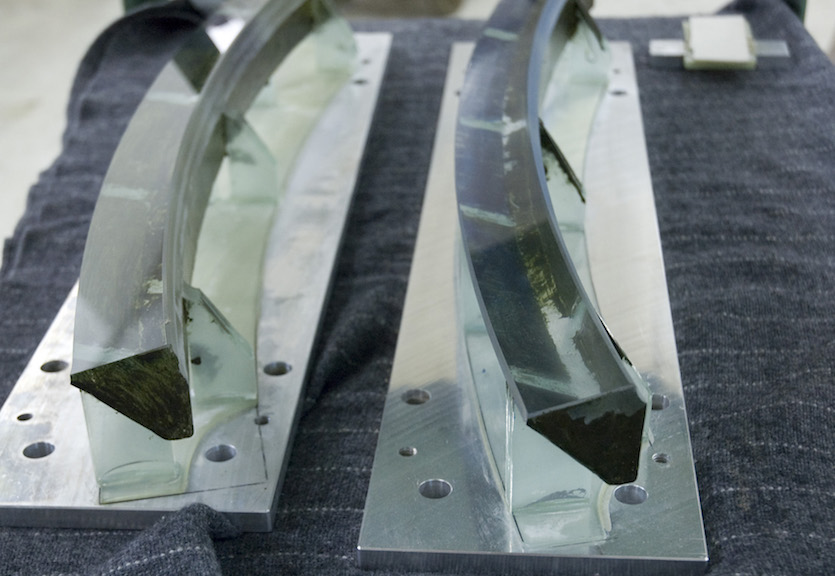
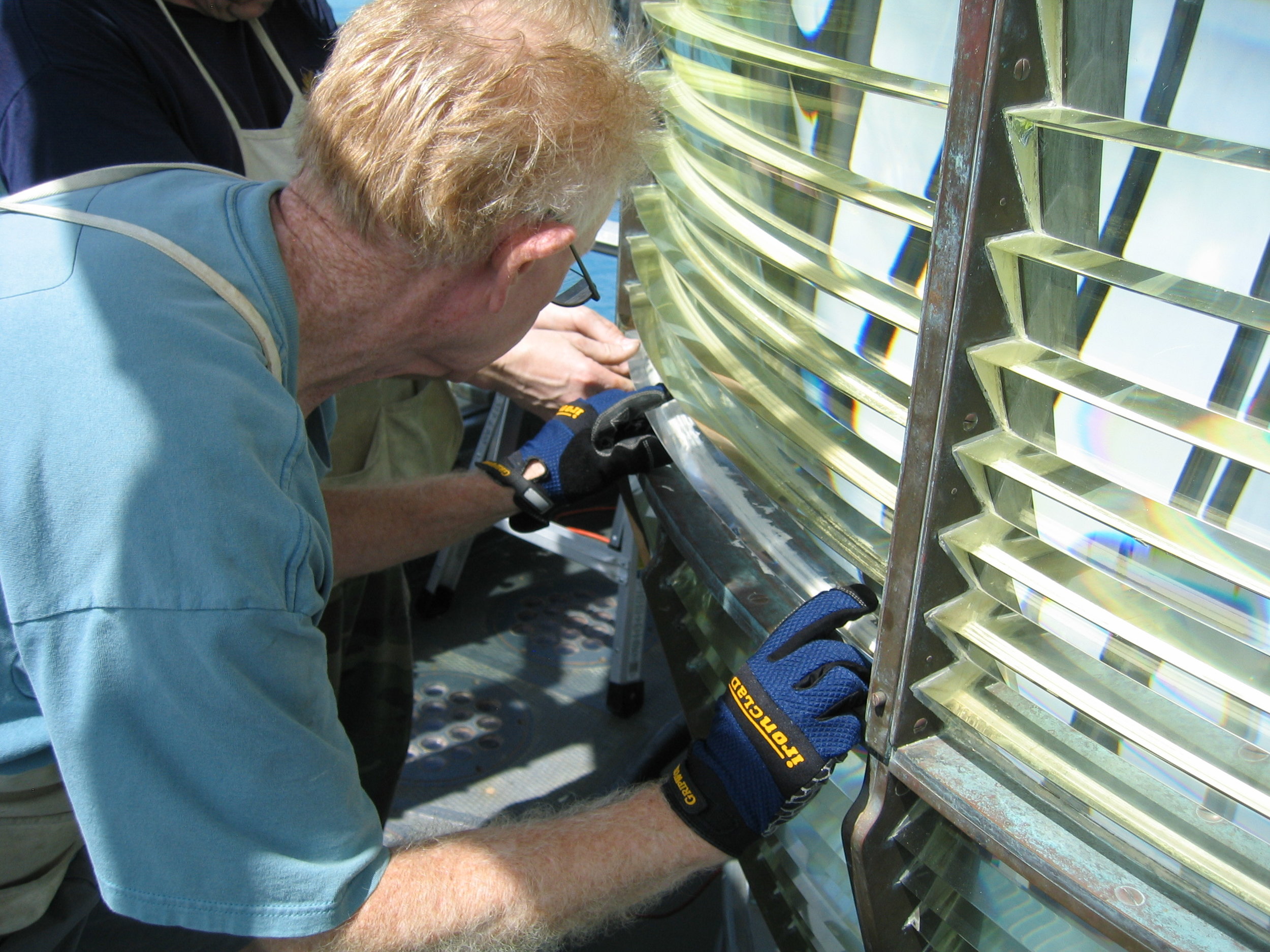
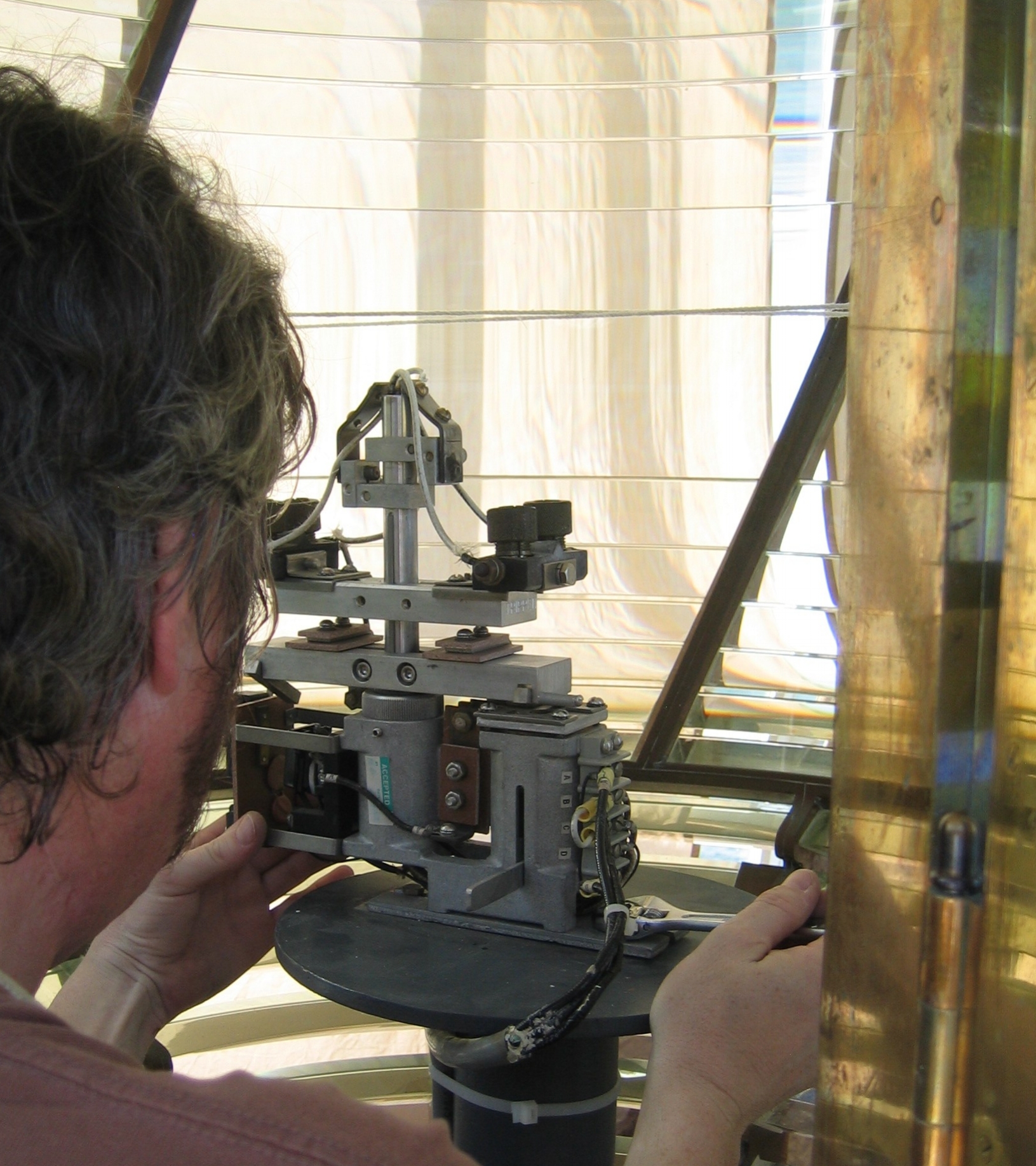
